中部地区のCHワイヤ、冷間圧造品メーカーのセントラルヨシダ(本社・愛知県あま市森1―4―1)は今年、創業100周年を迎えた。洋釘の製造事業からスタートし、時代のニーズに合わせて生産品目を変えながら、高い製造技術とQCD対応力を武器に数多くのユーザーを獲得。製造業が集積する中部地区のリーディングカンパニーとして、主要仕入れ先の神戸製鋼所と協業の下、1世紀にわたって自動車をはじめとする各産業を支え続けてきた。近年では日・米・タイ3拠点での生産によるジャストインタイムの供給体制を構築し、発展を続けるセントラルヨシダの歩みを振り返る。(佐野 雄紀)
創業期・洋釘製造通じ基盤固め
20世紀初頭、国策として官営八幡製鉄所(現・新日鉄住金)が釘の母材となる線材の製造を開始。この素材を使用し、安田商事(現・安田工業)が東京・深川区で洋釘の生産を始めたことが釘の国産化の始まりだ。
大阪でも釘の生産が盛んになる中、釘製造用の設備を製作するため創業者・吉田俊次氏が1917年に立ち上げたのがセントラルヨシダの礎、吉田製鋲所。その後設備製作のノウハウを生かして釘の製造、販売も手掛けるようになる。
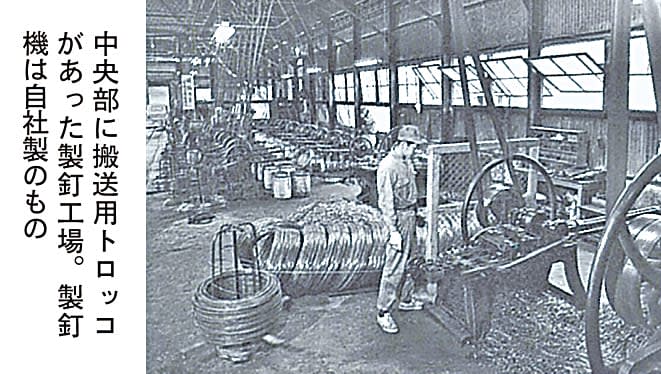
19年に名古屋市西区菊井町へ工場を移し、洋釘や製釘設備の製造を始めた最中の23年に関東大震災が起こった。釘の大型特需が発生する中で東西メーカーの供給能力が不足。丸釘が大量に輸入される一方、中部随一の釘メーカーだった吉田製鋲所に引き合いが集中し、生産数量を一気に伸ばした。
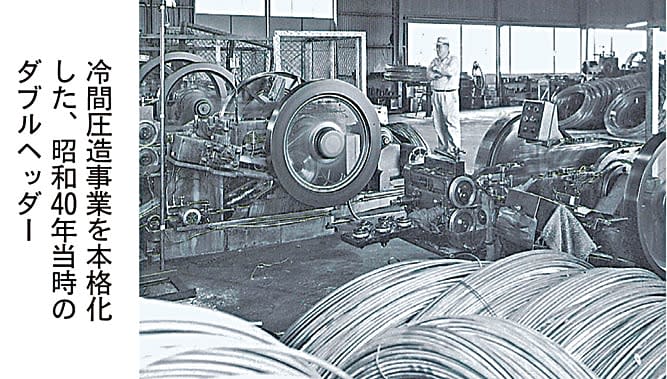
32年には現在の名古屋工場所在地、名古屋市中川区富船町へ本社を移転。中川運河沿岸初の工場として操業をスタートし、続く36年から特殊線材をベースとする硬鋼線製造事業に参入した。このころ俊次氏は愛知県硬鋼線統制組合理事長を務めるなど、業界にも大きく貢献している。
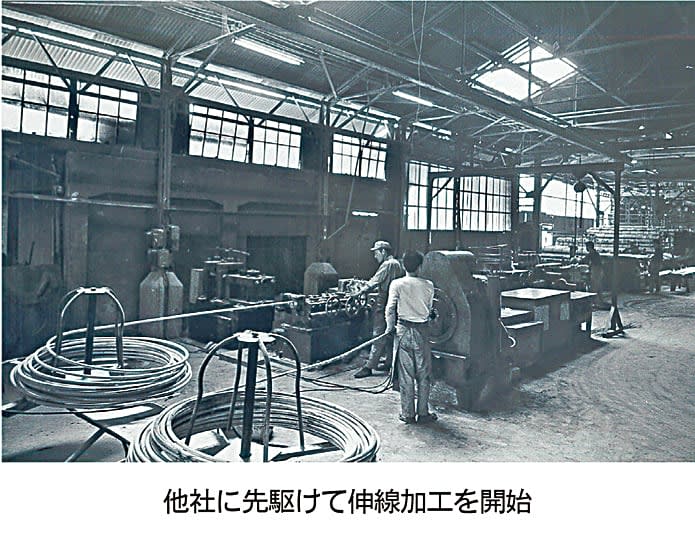
第二次大戦により建屋の半分が焼失したものの、被災工場を再建して事業を再始動。48年に吉田製鋲所の権利義務を承継し、資本金1千万円で吉田製線工業を設立した。翌49年には神戸製鋼所系列の加工メーカーとなり、52年からはアメリカ向けの釘輸出を開始(月2万トン)。一気に業容拡大を加速する。
成長期/CHワイヤ・冷間圧造品事業へ参入
戦後住宅向けなどの普通線材および普線製品のニーズが高まると同時に、モータリゼーションの加速に伴って自動車部品関連の需要が急拡大。1950年代から自動車部品メーカーと取引関係がスタートする。
しかし普通線材を母材としたことから、強度不足で割れが生じる、ねじ頭が欠けるといったエラーが続発した。そこで、冷間圧造に適した2次加工技術の開発に乗りだす。
焼きなましを行い、表面潤滑材を塗布するといった工夫を重ねて表面潤滑性、内部組織、寸法精度の各条件を満たした冷間圧造に適する線材を造り上げ、55年、冷間圧造用ワイヤおよび冷間圧造製品の生産開始に漕ぎ付けた。なお、翌56年には神戸製鋼所が冷間圧造用素材「KCH線材」の開発および量産体制を構築している。
連続伸線設備を導入し、増資も行うなど徐々に伸線メーカーの地位を築き上げ始めた矢先、59年に伊勢湾台風が中部地区に上陸。工場や設備の被害は免れたものの、従業員が被災したことから1カ月の操業停止に追い込まれる事態となった。
逆境を超えて自動車関連製品の需要が国内以上に広がりを見せていたアメリカへの線材輸出を始めるとともに、69年には大同製鋼製のCHワイヤ用連続焼鈍炉を日本で初めて導入。釘の生産を中止し、高級路線への一本化を図った。
線材加工を本格始動してからの約60年間、ユーザーである大手自動車部品メーカーや神戸製鋼所、新日鉄住金をはじめとする素材メーカーとの継続的な協業により、同事業はグループの核に、そして成長の原動力となり続けている。
業容が新たなステージに突入する中、俊次氏の婿養子に当たる吉田圭逸氏が独立し、三井物産とタッグを組んで70年にセントラルメタルを設立した。アメリカ向けを中心とする高級線材の輸出をスタートしたが、結果的に吉田製線工業と競合関係に。両社が協議を重ねた結果、互いの発展を目指した合併を決断。75年にセントラルヨシダが誕生し、圭逸氏が初代社長に就任する。
発展期・海外拠点開設
82年にスラグフォーマーOBF380Dを設置してスラグの本格生産を開始。太径材を母材とするスラグを伸線から一貫加工し、ファスナーメーカーへは細径素材を供給するという現在の事業モデルを確立した。
一方、主要ユーザーの自動車業界では対米自動車輸出自主規制により輸出台数が頭打ちに。85年のプラザ合意で急速に円高が進行、輸出の採算が悪化するなど、アメリカへの販売戦略の見直しを迫られていた。
自動車、自動車部品メーカーは現地生産に乗りだすため海外進出を加速。この動きに対応し、日本の自動車企画に適う高品質のCHワイヤ、圧造製品を適正価格・安定供給することを狙って88年、ノースカロライナ州に工場用地40万平方メートルを手当てした上で「ブルーリッジメタルズ(BRM)」を立ち上げた。
伸線・冷間圧造・熱処理工場1棟、酸洗工場1棟を建造して一連の生産設備を入れ、90年から本稼働に移行した。日本基準の品質・コスト競争力・納期管理を徹底し、日系ユーザーの信頼を獲得。92年にはフォード社への材料納入指定業者の資格を得ており、現在ではアメリカに拠点を置く各国メーカーと取引を重ねている。
90年代から2000年代初頭にかけ、経済水準の向上と消費人口の増加を背景に、自動車の次なる需要地として東南アジアがフォーカスされる。すでに自動車の現地生産が一般化する中、自動車関連メーカー各社はこぞって組立工場の建設に取りかかった。
ユーザーへの即納体制強化とさらなる数量拡大を目指し、11年に2番目の海外生産拠点となる「CYC METAL(CYCM)」(チョンブリ県アマタナコン工業団地)を設立。現地ニーズの拡大に合わせて徐々に機能強化を進め、2014年には、伸線~圧造までの一貫体制を構築するに至る。
日系メーカーの現調化に伴う受注を相次いで獲得し、ステンレス線材を母材とした排気系部品を100万個単位で展開する主力事業では、圧造から機械加工までの一貫生産を手掛ける。今後も設備投資を重ねながら、対応力に磨きをかける方針だ。
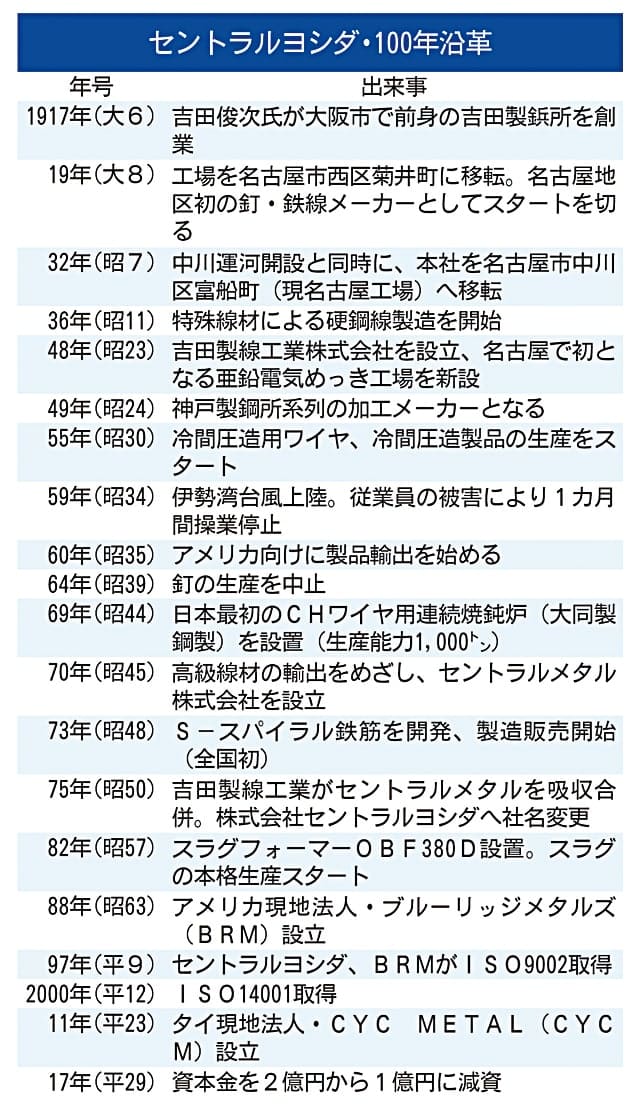
次の100年に向けて
地区初の釘メーカー、線材へのシフト、海外進出を経て1世紀の時を駆け抜けたセントラルヨシダだが、吉田篤史社長は事業の継続、拡大に向けた課題を口にする。それは事業範囲やエリアの拡大、海外拠点の生産性・収益性向上、ブランディング活動の強化だ。
しかし、どの局面でも市場動向を捉えた上で積極的な変化を遂げながら、ユーザーの要求にきめ細かく対応する姿勢を貫徹、ステップアップするところに同社の強みがある。
自動車業界は現在、為替や通商問題に伴うメーカーの世界的生産戦略、EVやPHVの普及観測による部品の仕様変更など目まぐるしい変化の最中にある。セントラルヨシダは今後もこうした「波」を的確に読み、これに上手く乗りながら成長し続けるだろう。
吉田篤史社長に聞く/時代、需要に合わせ事業展開/自動車市場とともに成長
――創業から1世紀という大きな節目を迎えました。
「国内自動車市場の拡大に合わせて段階的な成長を遂げることができたが、これは長年取引関係にある自動車部品メーカーなどのユーザー、神戸製鋼所や新日鉄住金などの素材メーカーの存在があってこそのこと。皆様の支えにより100周年を迎えられたことを心から感謝したい」
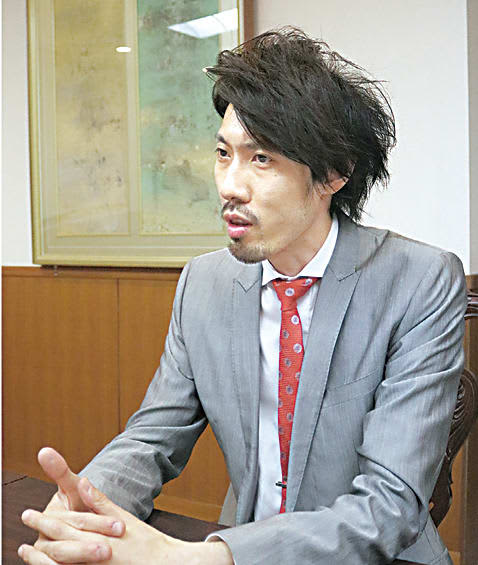
――改めて現在の業務内容、拠点などをお聞かせ下さい。
「国内2工場に加えてアメリカにBLUE RIDGE METALS(BRM)、タイにCYC METAL(CYCM)を設立。自動車向けを中心とするCHQワイヤ、冷間圧造品の生産を手掛けており、月間の鋼材取扱量は日・米・タイを合わせて1万2千トン、うち3500トンを圧造品として出荷している」
――100年間にわたって持続的成長を遂げられた要因、ターニングポイントはどこにあるか。
「大きく3つの転換点がある。当社は大阪で創業した吉田製鋲所がルーツ。当時国内では、洋釘の国産化が国策として進められており、名古屋で最初の洋釘メーカーとしてスタートした。最初の大きなターニングポイントは創業から間もない1923年に発生した関東大震災。大規模な家屋倒壊によって釘の特需が発生し、創成期の業績を大きく押し上げた」
「2点目は建築用製品から自動車用製品への事業シフトだ。昭和20年代から自動車関連ユーザーの引き合いを受けていたが、普通線材では、強度や製品精度を満たせなかった。そこで、冷間圧造に適した、柔らかく滑りの良い線材の加工工程を独自で開発、その後素材メーカーである神戸製鋼所が現在の冷間圧造用素材の開発に成功した。それからの60年は、素材メーカーと一体となって改善・成長してきたという歴史がある」
「最後は生産拠点をグローバル化して以降、現在までの30年。日系自動車メーカー、部品メーカーの現地調達化や米系メーカーの取り込みを狙い、88年にBRMを設立。2011年にはCYCMを立ち上げ、国内市場が縮小傾向を辿る中でもグループ一体で業績を伸ばすことができた。創業者の俊次氏、二代目・圭逸氏に先見の明があり、支えてくれる社員がいたからこそ、現在の当社があると言える」
――事業を拡大する一方、苦境に立たされた局面は。
「69年に日本で初めてCHQワイヤ用の連続焼鈍炉を導入したが、投資金額は当時の月間売上高と同等の1億円に上った。線材需要の拡大を予想した設備導入ながら、工場を担保に入れての大投資で社内からも相当の抵抗があったようだ」
「08年のリーマンショック発生時は、主力製品の一つである排気系部品の受注がゼロとなった。数十もの加工ラインが停止、年間での赤字計上を余儀なくされた」
――近年、今後の線材二次加工業界をどう見ているか。
「部品メーカーのノックダウン生産は底堅い水準ながら、内需は自動車生産台数の減少に伴い縮小。二次加工メーカーによるユーザー動向に合わせた海外投資が続くと思われる。部品点数の少ない電気自動車の台頭により車種構成の変化は見込まれるものの、自動車市場全体の持続的成長を加味すると、二次加工の全体量はほぼ横ばいで推移すると見込んでいる」
――足元課題と捉えている点は。
「1955年以降線材加工業で成長を遂げてきた一方、60年以上事業モデルが変わっていない点に一定の危機感を持っている。長期的には国内の線材需要が拡大する可能性が低い以上、事業領域の拡大を本格検討すべき局面にあるだろう。自動車関連ユーザーの動向を敏感に察知し、付加価値の拡大を図ることが不可欠だと考えている」
「労働者人口の減少も大きな問題。人手不足によってオペレーションが機能せず、高品質品を安定供給するという現在の『当たり前』の体制が崩れる危険性が急激に高まりつつある。段階的に福利厚生をより良いものへ変えて社員の定着率向上を図るほか、作業の標準化・平準化や、国内から海外、海外から国内といった柔軟な生産シフトを検討するなど、多角的方法を通じて、需要に対応し続ける生産体制を維持したい」
――今後の飛躍に向けてカギとなる点、注力するポイントは。
「上述の〝人〟が最大のカギとなるが、次に重要なのが設備能力や環境面の課題解決である。近年タイ・CYCMを中心とする海外拠点の増強を積極化してきたが、受注拡大や工場・設備の老朽化に伴って本社工場へ設備投資する必要が生じている。特に熱処理工程への投資が急務であることから、3年内をめどに熱処理炉の増設、連続炉のリプレースを実施する計画だ。それ以外の工程でも設備のオーバーホールや買い替えを順次行っていく」
「また、需要家が海外展開する中で、当社も、国内・世界に向けたさらなる知名度向上を図ることが重要だと考える。100周年を機に、さまざまな形でのブランディング活動を行って人不足に先手を打っていきたい」(佐野 雄紀)