東京製鉄岡山工場(岡山県倉敷市、工場長・國米博之氏)の製鋼設備は現在150トンの直流(DC)電気炉と炉外精錬設備(LF)が各1基、スラブ用の第3連続鋳造機(3CC)とブルーム用の第4連続鋳造機(4CC)を備える。
従来、中形と棒鋼の2つの圧延工場には140トンの交流(AC)電気炉からブルームを供給していたが、AC炉は1978年の稼働から約40年が経過し、主幹部の老朽化やトランス更新が課題となっていた。このため、ホットコイル生産を田原工場(愛知県)に集約した2015年4月から休止中だった150トンDC炉へ製鋼設備を切り替えた。
DC炉は1992年稼働とAC炉に比べ新しい設備で、1時間当たりの出鋼能力は約210トンとAC炉(同約100トン)の約2倍。電力消費原単位を約6%削減できるほか、水処理など付帯設備の稼働時間も減らせるため、省エネとコスト削減のメリットが見込める。
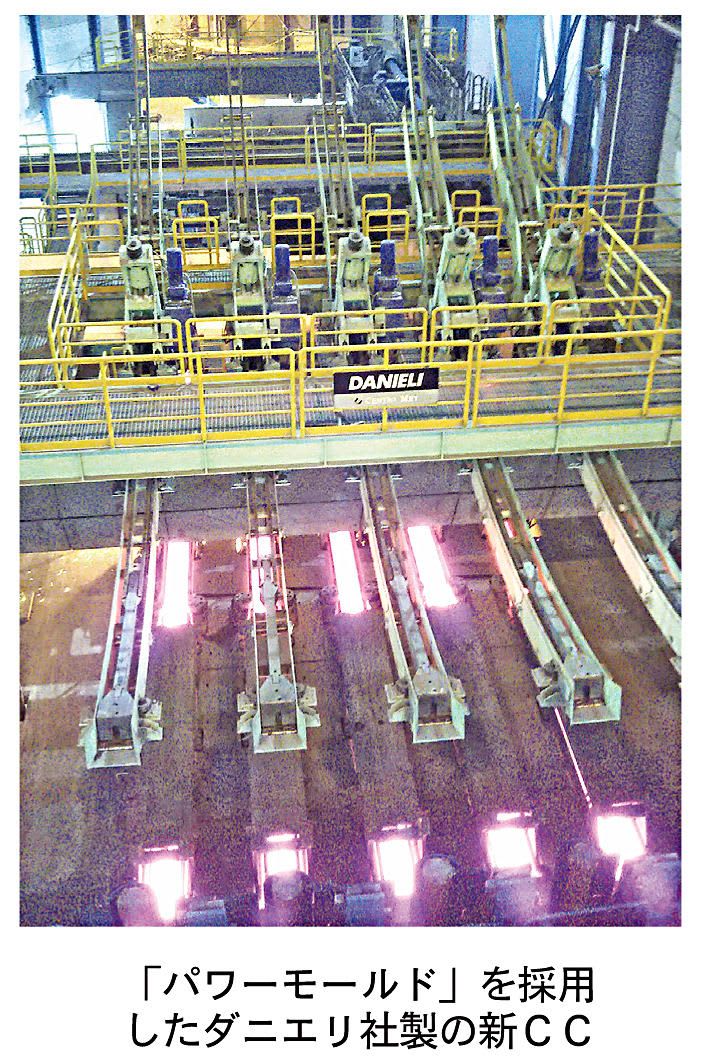
一方、DC炉は熱延工場にスラブを供給する設備だったため、中形や棒鋼工場にブルームを供給するには新たなCCの導入が必要。しかも「1時間当たり210トンというDC炉の出鋼能力を受け止められる高速なブルームCCが必要だった」(國米工場長)。
DC炉への切り替えを図るため、製鋼工場には新たにダニエリ社製のブルームCCを導入した。4CCと呼んでいる新CCは5ストランドの湾曲型で、鋳片サイズは170ミリ×170ミリ、225ミリ×225ミリ、250ミリ×310ミリの3サイズ。
新CCの特徴としてまず挙げられるのが、1時間当たりの生産能力の高さだ。170角のブルームの場合、引き抜き速度は分速3・5メートル。旧AC炉のCCでは同2・2メートルが限界だったため、4CCの引き抜き速度は約6割ものアップとなる。
通常、CCでは鋳込み速度を上げるほど、破裂して溶鋼が漏れ出すブレークアウトの可能性が高まるとともに、内部に割れが生じやすくなる。
しかし、新CCは高速で鋳込みつつも内部品質は良好。ダニエリ社製の新CCには「パワーモールド」という特許技術を用いた特殊なモールドが採用されており、溶鋼を通す銅管を冷却制御する高い技術力が高速鋳込みと良好な内部品質を両立させている。
國米工場長は新CCについて「分速3・5メートルの高速鋳込みでも内部欠陥のない高品質なブルームが安定生産できている。品質維持が可能な生産の限界速度を上げられた」と高く評価している。
4CCは昨年11月4日にホットラン。順調に立ち上がり、製鋼はDC炉での生産に移行した。4CCは製鋼工場の3CC横のわずかなスペースを有効活用して設置されており「この狭い所によく収まったなと驚かれる」(國米工場長)という。また、ブルームの管理を容易にする狙いもあり、以前の4サイズ(170ミリ×170ミリ、170ミリ×235ミリ、220ミリ×250ミリ、250ミリ×310ミリ)から3サイズに集約した。
岡山工場の生産量は条鋼類が年45万トン強、田原工場のホットコイルを母材とする鋼板の下工程(酸洗、冷延、めっき)が年15万トン。粗鋼ベースの生産量は月間4万トン前後。
DC炉の稼働で岡山工場の製鋼能力には月間3万トン強の余力が生じる。この能力は田原工場向けのスラブ供給などに振り向け、ホットコイルの生産量を増やす計画。このため、今月17日にはスラブ用の3CCを約3年ぶりに再稼働させた。今後はJISの維持審査などを経て、4月にも本格生産を開始する。
中形や棒鋼の圧延能力は1時間当たり80~90トン程のため「DC炉はスラブCCが稼働して初めて本領を発揮できる」(國米工場長)とする。3CCと4CCの切り替えは約3時間で可能なため「土日フル操業時の在庫状況などを勘案しながら柔軟に生産していく」(同)とした。
今後、岡山工場では条鋼と半製品のフルトラッキング設備を年内に順次導入していく。製鋼から出荷までの識別管理を自動化し、トレーサビリティ体制を整える狙い。また、将来的にはスクラップヤードの入出庫管理から配合までの自動化システムを導入し、省力化を図っていきたいとする。「そこまで出来れば岡山工場はかなり筋肉質で競争力の高い工場になる」(國米工場長)と語っている。(小堀 智矢)