NGKファインモールド(本社・愛知県半田市、社長・石原敏明氏)は、日本ガイシの金型事業の中核を担う金型メーカー。素材調達、設計からワンストップで対応可能な体制を武器に、主力向け先である自動車の部品樹脂化進展も追い風に、高い稼働状況が続く。近年では旺盛な需要に合わせた設備更新を積極化し、ベリリウム銅を使用した熱伝導率の高い「ハイサイクル金型」を開発、本格的な拡販にも乗り出した。成長に向けて新たな歩みを始めた同社の今をルポする。(佐野 雄紀)
NGKファインモールドは、日本ガイシが金型事業部門の営業機能、設計および機械加工機能をそれぞれ分社化後、1996年までに関連会社を一本化して誕生した。
日本ガイシ・金属事業部の主要生産拠点、知多事業所と1キロほどの至近距離に位置しており、ベリリウム銅素材供給や開発、営業活動、人事交流をはじめとする円滑な協業を実現している。
ユーザーは自動車関連が8割以上と大多数を占め、生産品目も内外装部品向けのプラスチック金型、タイヤ成形用金型が中心だ。
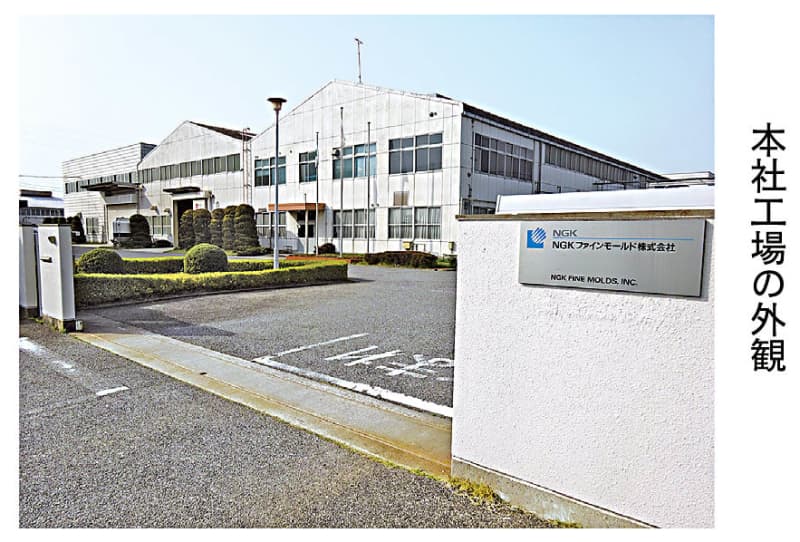
構内二つの工場棟のうち、プラスチック金型の建屋面積は約3500平方メートル。三次元CADで設計、CAMで加工条件設定後、まず金型用鋼材をマシニングセンタ(MC)で機械加工する。試作品用射出成形機を13年に入れ替え以降、MCは17年に1台を更新、今後も生産性、精度向上を図った新設備を導入する方針。
一つの金型製品に対する総部品点数は500点に上るケースもあり、製品形状によりアンダーカットになる部位には一品一様の「入子(いれこ)」をセットする。現在この「入子」にベリリウム銅を使用することによって局所的に製品冷却を促し、サイクルタイムを短縮する方式が主流となっている。ただ生産性アップに向け、より広範にベリリウム銅を使用する金型へ移行しつつある。
同社はこうしたニーズを捕捉し、販路拡大にも努めた上でハイサイクル金型の売上高を3年間で倍増させる計画を立てる。また、部品のモデルチェンジによって繁閑差が生じることから、稼働状態の平準化策も検討を重ねる方針だ。
タイヤ成形用金型は鋳造用アルミ合金を素材とし、約2千平方メートルの工場で生産する。15年に日本ガイシ・知多事業所から鋳造工程を移設、設計から金型完成の一貫体制を構築した。
型の製作に当たって、まず合成樹脂素材を5軸MCで切削し、タイヤの完成形状を模した「マスターモデル」を製作する。この工程のMCも16年に3台リプレースするなど、各所でハードの増強を重ねている。
同製品はマスターモデルをもとにゴム型、石膏鋳型を製作し、これにアルミ溶湯を鋳込んで、円形の「トレッドリング」を成形するのが基本的な流れだ。しかし、タイヤの細溝を形作るためにステンレス製の小板「ブレード」を型に入れる必要がある。
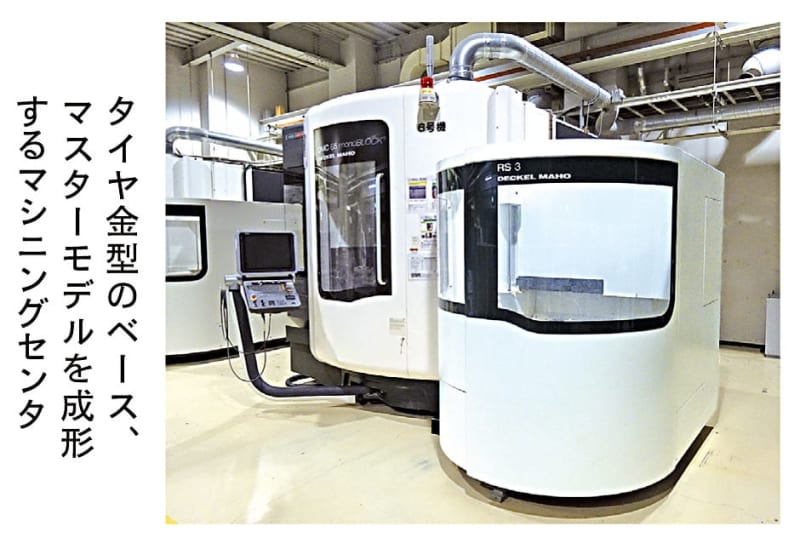
一製品で500枚に上る場合があるブレードは、タイヤの安全性を左右する重要要素。タイヤ成形時の圧力で外れないように、鋳造と同時に金型へブレードを埋設する「鋳ぐるみ工法」を用いて高い強度を保つ。
鋳造したトレッドリングはターニング加工機(縦型旋盤)で外径加工を行い、タイヤ幅方向で数個に分割、最終の完成金型まで一貫対応することで短納期対応を可能としている。
日本ガイシとの連携によるユーザー拡大を通じた、ベリリウム銅使用のプラ金型の拡販をスタート。業績伸長に伴う生産設備の更新も進め、NGKファインモールドは製販のレベルアップへの取り組みを本格化する。
今後高い品質に一段と磨きが掛かり、底堅い需要環境も支えとなり段階的な成長を遂げそうだ。