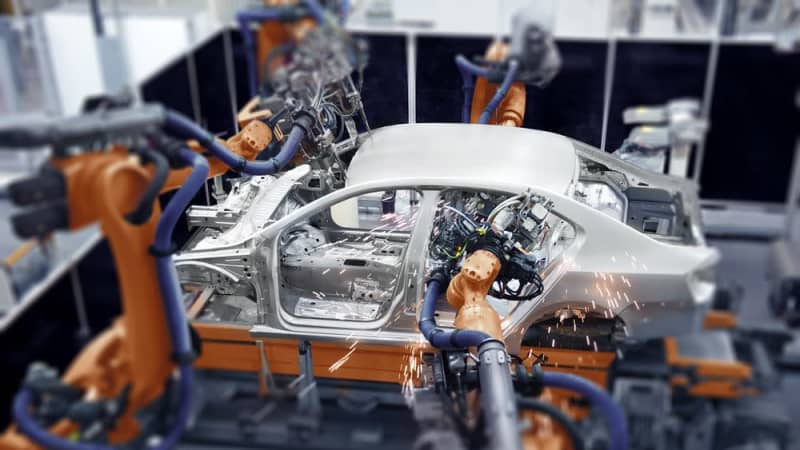
脱炭素が世界の潮流となり、世界の自動車業界で電気自動車(EV)シフトが本格化している。しかし、日本の自動車メーカーと欧米の自動車メーカーでは、EVシフトの進め方に違いがあるようだ。全面的なEVシフトに舵を切り、EV専用工場の建設を進める欧米勢に対して、ホンダを除く日本の自動車メーカーは、ガソリン車やEVなど多様な選択肢を維持するため、混流生産の高度化を進める。市場の変化に柔軟に対応するための取組みの最前線を見てみよう。
目次
- EV組み立てを自動化するニッサンインテリジェントファクトリー
- モジュール化で混流生産にも対応
- マツダは、パワートレーン取付けにAGVを活用
- 海外では、EV専用工場の建設が進む
EV組み立てを自動化するニッサンインテリジェントファクトリー
日産は、次世代の自動車生産のコンセプトとして「ニッサンインテリジェントファクトリー(NIF)」を掲げる。ロボットによる自動化やCO2削減と仕上がりの向上を両立した塗装、工場全体のネットワーク化による予防予知保全やリモートメンテナンスなどの生産技術により、CASEやカーボンニュートラルへの対応を進める狙いだ。NIFの導入第一号である栃木工場では、次世代EVアリアが生産されている。
組み立て工程の自動化を支えるのが、「SUMO(Simultaneous Underfloor Mounting Operation)」と名付けられたパワートレーン一括搭載システムだ。パワートレーンとは、車のエンジンや、エンジンで発生した回転エネルギーを効率よく駆動輪に伝えるための装置類のこと。SUMOは。パワートレーンのユニットを車のボディに取りつける作業を自動化する。ハンガーで車体を吊るして置き、その下から、パレットに載せたパワートレーンのユニットを上昇させ、一気に取りつける。その際には、吊るされたボディの位置をカメラで測定し、それに合わせてパワートレーンの角度を補正することで、高精度の取付けを実現している。最後に、ロボットでボルトの締め付け作業を行い固定するが、ボルトの供給も含めて、作業の全てが自動で行われることが特徴だ。
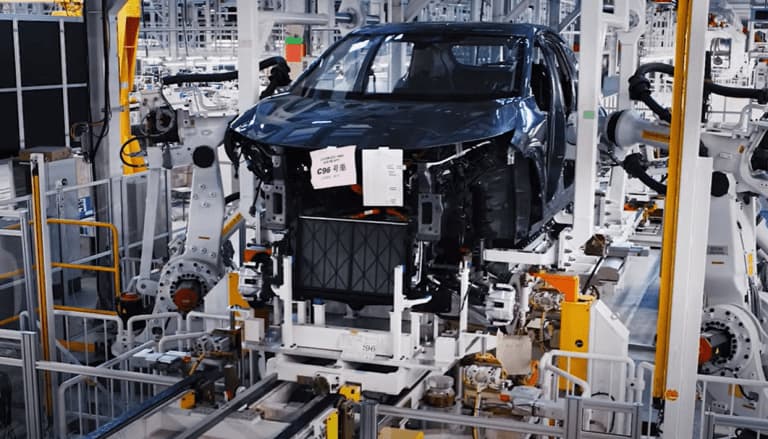
これまでは、作業員がリフターを使ってエンジンなどを持ち上げ、位置合わせをして手動で取り付けていたが、腰を曲げて上を向くような高負荷の作業のため、1日に数百台がラインを流れると作業者の体の負担が大きくなってしまう。SUMOによって、このような負担が解消されるのだ。
モジュール化で混流生産にも対応
アリアには、バッテリーと駆動方法の組み合わせが4種類あるが、NIFでは一つの設備で全てに対応することが可能だ。現在、栃木工場で生産されているのはアリアのみだが、SUMOはパレットのモジュール化により、ハイブリッド車やガソリン車のパワートレーン取付けにも対応する。SUMOで使われるパレットは二層になっており、全車共通のベースパレットに、交換可能なフロント、センター、リアの3パレットを重ねる構造になっている。上に載せるパレットの組み替えることで、多様な車種を混流生産することが可能になるのだ。従来は、ガソリン車と電気自動車を1つのラインで流そうとすると、ガソリンタンクの搭載工程で電気自動車は手待ちになってしまい、混流生産時のロスが課題になっていた。SUMOでは、モジュール化によって異なるパワートレーンを持つ車両を同一の工程でロスなく生産できる。
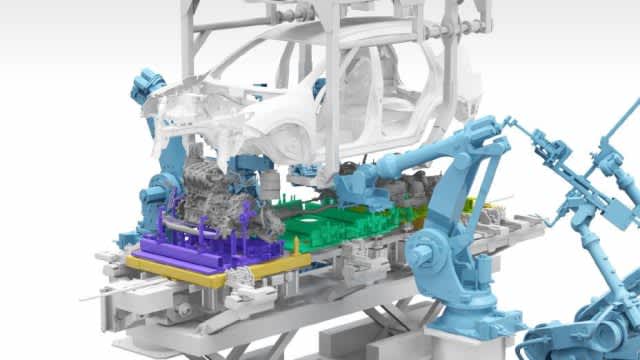
マツダは、パワートレーン取付けにAGVを活用
同様に、モジュール化を進めて混流生産を進めるのがマツダだ。マツダの世界シェアは2%に満たない。従来のガソリン車やディーゼル車の生産も続けつつ、EV生産も進めるためには、多品種少量生産の技術を磨いてくことが不可欠といえる。マツダは、全車共通の「固定要素」については、汎用設備を活用する。そして、車種によって異なる「変動要素」は、モジュール化した設備で対応する。これにより、エンジン車であってもEVであっても、また、車体の大きさが異なる車であっても、同じ生産ラインで製造することが可能になった。
大きさの異なる車種のパワートレーンの取付けには、AGVが活躍する。ボディを上から吊り下げるところまでは、日産のNIFと共通だが、マツダの場合は、パワートレーンを運ぶのはAGVだ。小型車の場合は、AGVの距離を詰めるなど、AGVの位置とそれぞれの距離を制御することにより、全ての車種のパワートレーンの取付けに対応する。2021年にAGV導入などの改修を行った防府第2工場では、セダン「マツダ6」やスポーツ多目的車「CX-5」を生産する。マツダでは、今後、2025年までに発売予定のEVや、プラグインハイブリッド車など、複数車種の混流生産を進める予定だ。
マツダでは、汎用設備の開発や工程のレイアウト検証に、デジタルツインを活用している。仮想空間上で様々なシミュレーションを行うことで、リードタイムの削減やコスト削減を実現する。混流生産やデジタルツインなどによる改革の結果、マツダでは、新車製造のための生産ラインの構築に必要な期間を、従来の1/5、そして、費用はなんと従来の1/10にすることに成功したという。
さらに、同一工場での混流生産に加えて、複数工場で同車種を平行生産できるようにする取組みも進める。これにより、想定以上に特定の車種が売れるなど、一時的に生産を増やす必要がある場合に、柔軟な対応が可能となる。コロナ禍で、一つの工場での生産を止めざるを得ないような場合にも効果的だ。
海外では、EV専用工場の建設が進む
ドイツのVWグループは、2025年までに150万台のEV生産を目指しており、生産能力の増強が急務となっている。生産能力強化の一環として、ガソリン車やディーゼル車の製造を行ってきたツヴィッカウ工場を、EV専用の工場へと改修した。あわせて、シーメンスのIoT基盤「MindSphere(マインドスフィア)」を導入するなど、大規模なデジタル化を進めている。
GMは、ミシガン州デトロイトのハムトラミック工場を全面改修し、2021年11月にはEV専用工場の「ファクトリー・ゼロ」として操業を開始した。同工場では、ピックアップトラック「ハマーEV」や自動運転専用車の「クルーズ オリジン」などのEVが生産される。
最新の技術を活用し、ゼロベースでレイアウトを最適化できる専用工場にはメリットが大きい。しかし、EVの売上が伸び悩めば、専用工場はたちまち負の遺産となる。EVに賭ける欧米勢と、ガソリン車を含むあらゆる選択肢を残し、市場の変化に柔軟に対応できる日本勢。どちらのアプローチが吉と出るのか、答えは10年後に明らかになる。
(製造DXチャンネル 2022年5月23日掲載)